コスト削減に向けた動きが強まる昨今では、レーシングエンジンにも、高い耐久性と信頼性が要求される。それらを確保する上で、高性能な熱交換器は不可欠ともいえる存在だ。レース用熱交換器ならではの課題とは何か? その解決のため、設計者は何を考え、どのような手法を採るのだろうか?
TEXT:松田勇治(MATSUDA Yuji)
熱交換器は、エンジンが作動する上で利用している各種の流体を通過させ、その過程で流体が持つ熱を大気中に放出することで、温度を低下させる装置である。量産車エンジン用でも、レーシングエンジン用でも、装置としての役割はまったく同じだ。また、現在では熱交換に関する基礎的な技術が相当高度なレベルに達していることもあり、レーシング・エンジン用であっても、基本的な構造面は量産用とそう大きくは違わないという。
しかし、レーシング・マシンに特有の事情から、量産用とは異なる要件も存在する。たとえば、設計要件には「寿命」の検討が必要になる。量産車の場合、熱交換器そのものの経時による性能劣化は無視できるレベルだから、新車製造工程で装着されたものは、クルマの生涯を通じて無交換が基本だ。対してレーシング・マシン用の熱交換器は、コース上を周回するうちにフィンが飛石で潰れたり、タイヤかすが詰まってしまうことが避けられない。
そのような状態になったフィンが生じたチューブは、通風抵抗を減らすために列ごと折りたたむ。当然、その量が増えるにしたがって、熱交換性能は低下していく。スーパーGT用を例にあげると、だいたい3000kmの走行で30%性能が低下するという。
昨今はレース界でも経費削減の風潮が強まっており、定められた寸法、重量、コストの中で、いかに性能低下分のマージンを織り込んでおけるかが、設計者の腕の見せどころのひとつになるわけだ。
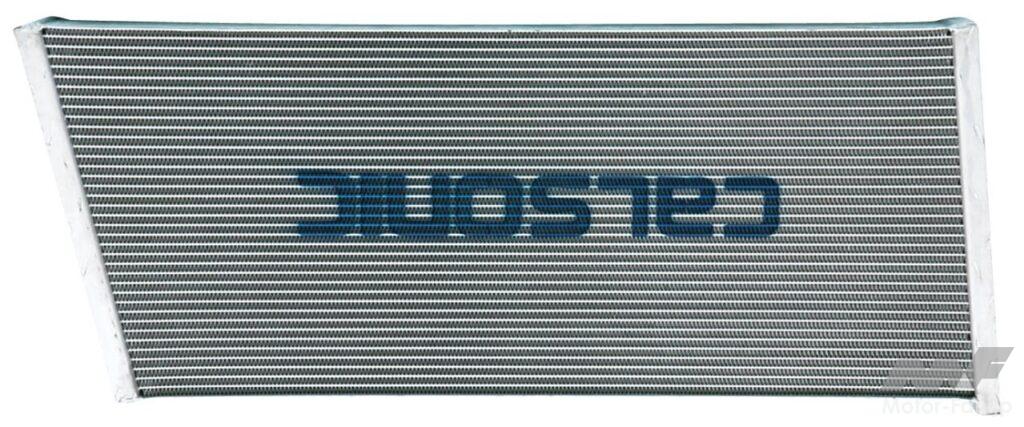
量産用とレース用で大きく異なる場合があるのは、その形状だ。特に純レーシング・マシン用では、空力面の要求から特殊な形状が求められることが珍しくない。対応のためには、製造技術に加えてシミュレーション技術などの面も重要となってくる。
レーシング・マシンの場合、インテークダクトの絞りや、内部で起こる渦流などの影響で、コアが本来持つ能力を100%発揮させることはできない。その点をふまえ、要求通りの形状を実現した上で、冷却性能に悪影響を与えないことが必要だからだ。
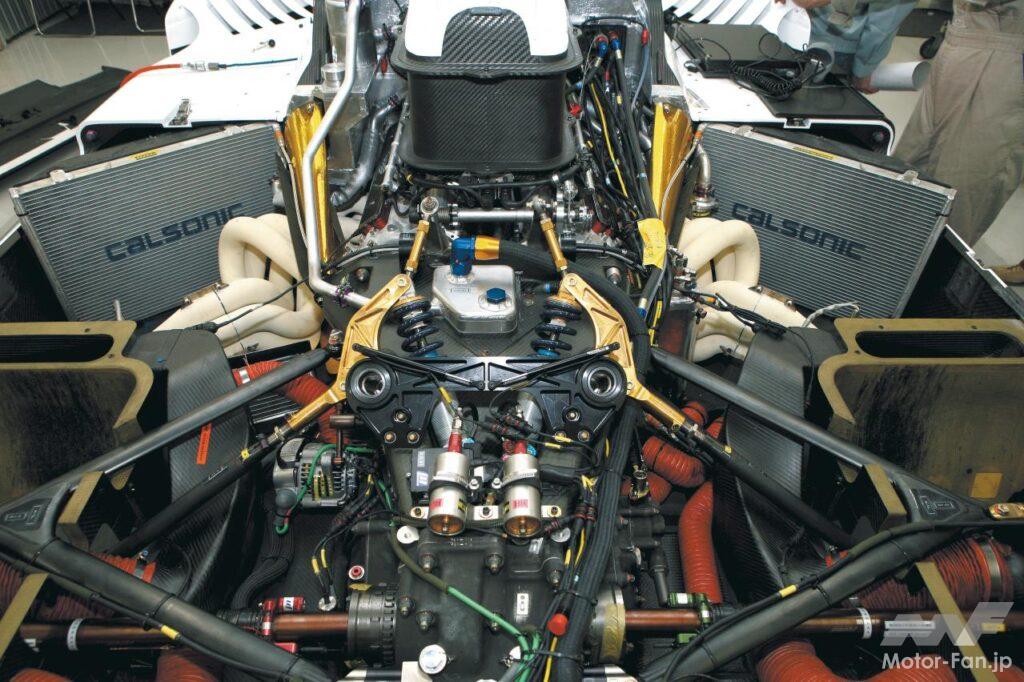
F1の熱交換器はどうやって設計しているか
ここまでは純粋に技術的な面の話であり、いわば常識の範ちゅうではある。例外はF1だ。カルソニックカンセイ(現・マレリ)は複数のF1コンストラクターへ熱交換器を供給しているが、彼らとの作業には、さまざまな“非常識”への対応が不可欠なのだという。
新規開発時のオーダーからして非常識だ。本来はエンジンが発生する熱量や使用温度域といったデータの提供を受け、それを前提として効率を高める方法を考えるのが熱交換器設計の第一歩なのだが、F1コンストラクターから、それらの具体的な数値が提供されることはない。
彼らから伝えられるのは、熱交換器を収容できるスペースのみ。つまり、「W×D×Hがこれだけの寸法の中で、どれだけの冷却能力を確保できるか?」だけだ。これでは、「オーダー」というより「問い合わせ」である。ひどい時にはW×Dだけの場合すらあるという。
F1の場合、複数の企業間に関わる契約上の機密事項が多数ある影響で、コンストラクター側はどうしてもこのような形でしかオーダーができないようだ。逆に言うと、とにかく限られた寸法の中で最も高い冷却性能を実現できるコアを確保しておき、その能力をベースとして冷却系、ならびに冷却性能に関わるボディワークの仕様を決めていく、という開発手法を採っているのだと推測できる。
F1用ラジエーターは、本体内に給水口もキャップも備えていない。エンジン側も含めた流路に冷却水を満たす作業は、専用ノズルからの真空引きによって行なう。その工程で冷却水に加圧しておくことで冷却水の沸点を高め、冷却性能を高める手法が一般的だ。おそらく5〜6bar程度の圧力がかけられていると見られ、その影響で、暖機完了後のラジエーターは目視でもわかるほど膨らむ。レース後、形状が元に戻っていく様は、「ラジエーターが呼吸をしているようにすら見える」という。この影響で、特に繰返し応力がかかる部分には、高い強度・剛性が必要となる。製造工程で熟練工の技が必要不可欠となる理由がそこにある。
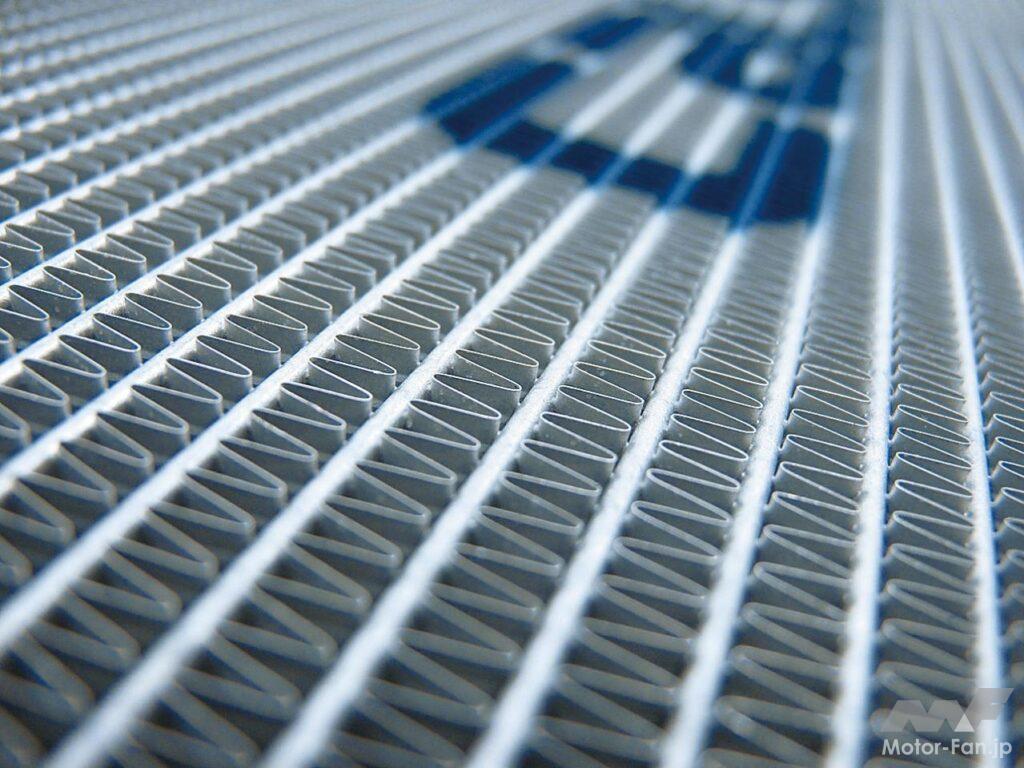
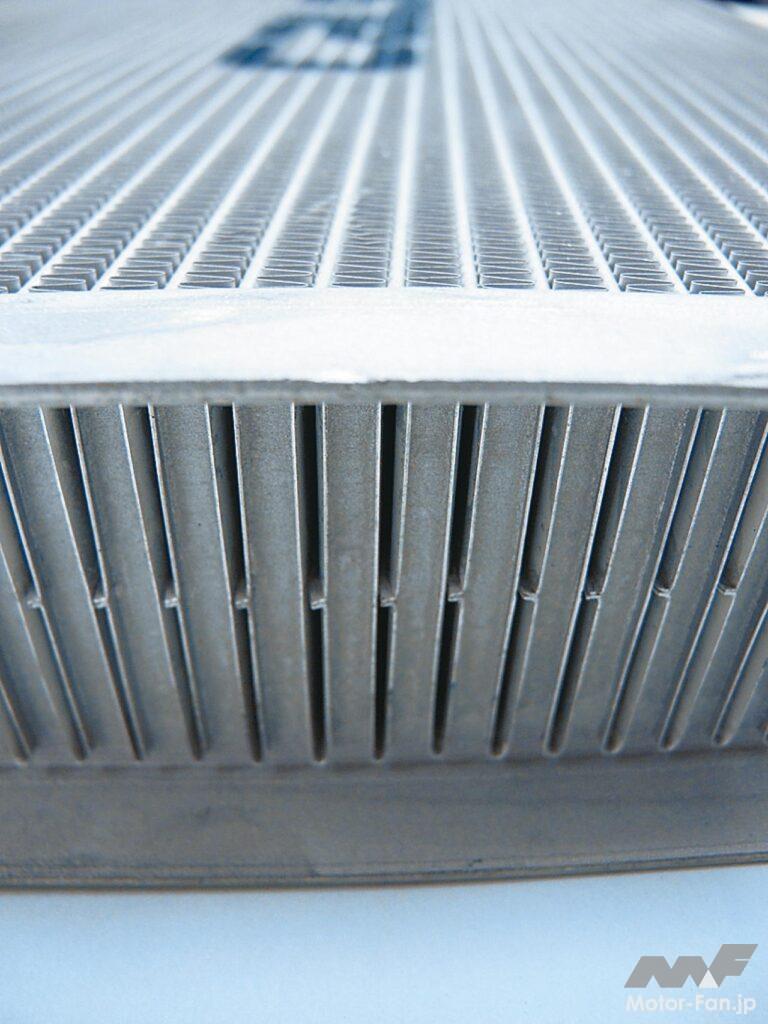
機密主義のおかげで、想定外のトラブルに見舞われることも少なくない。某コンストラクターに提供したオイルクーラーでは、まったく冷えないという深刻な事態に直面した。
エンジンを始動し、アイドル状態ではきちんと冷えるのだが、コースを1周してくる間にまったく冷えなくなってしまうのだ。原因を追求していくうち、エンジンオイルの性状の違いにたどり着いた。
熱交換器の性能を左右する指針のひとつに「滞留時間」がある。流体が熱交換器の中に入ってから出て行くまでの時間で、基本的にはこれが長いほうが冷却性能の点で有利になる。ただし、通流抵抗とトレードオフの関係になるため、ポンプの負担を下げる目的などから、用途によって設定を変える。
一般論として、ラジエーターは滞留時間を可能な限り短くしておく。オイルクーラーやインタークーラーは、ある程度の滞留時間があったほうが効率が高まるので、チューブ内部にルーバーを切ることで流路を長く、複雑化するなどしておく。
くだんのオイルクーラーもそのような構造だったのだが、オイルの粘度を量産用と同等に設定していたことが、冷却不良の原因だった。通常動作温度領域に達したF1エンジン用オイルの粘度は、量産用とはかけ離れたものだったのだ。この件については、後に「守秘義務から伝えられなかったとはいえ、申し訳なかった」との言葉があったそうだ。
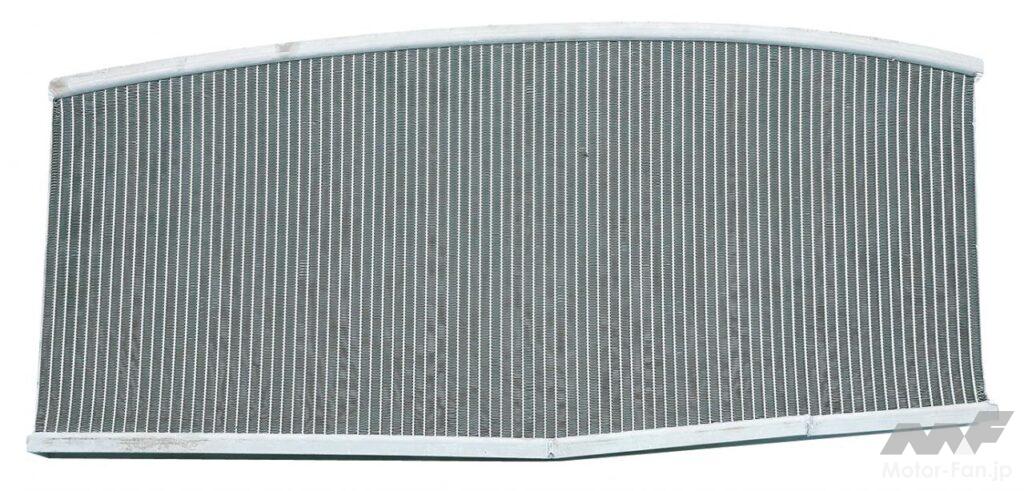
長年に渡ってそのようなやりとりを重ね、信頼関係が築かれると、ある程度の情報は開示されるようになる。たとえば、冷却水には「真水」を使う、といったことが伝えられる。これだけでも、開発側にとっては性能向上の上で貴重な情報だ。
ちなみに、2009年シーズン向けの開発では、どのコンストラクターからも口を揃えて「とにかく軽くしてくれ」と言われたそうだ。軽量化は絶えざるテーマだが、特に今年はKERS搭載による重量増加を少しでも補いたい、との意向がうかがえるエピソードではある。
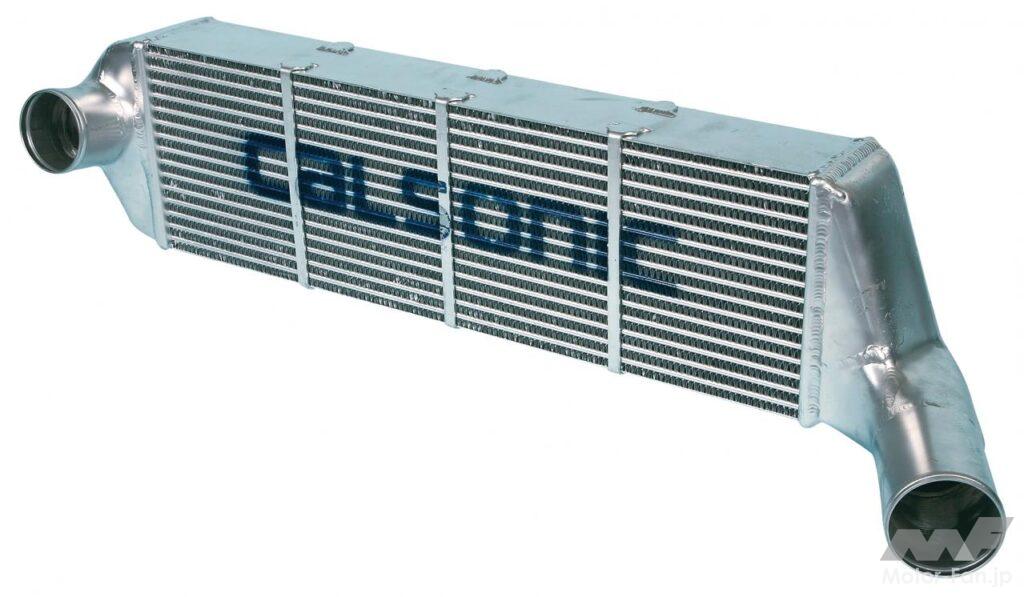
レース用熱交換器は、設計だけでなく、製造技術の面でも高いレベルが要求される。熱交換器はチューブ、フィン、外枠などの各のパーツを仮組みした状態で加熱、「ろう付け」によって完成させる。このため、加熱前の仮組み工程で、どこをどの程度押さえておくか?といった加減しだいで、完成状態の強度・剛性、変形を許容する方向とその度合いなどが大きく変わってくる。特に高圧にさらされることで大きな変形を許容しなければならないレース用熱交換器では、仮組み工程における力加減などの面で、熟練工の経験に基づいたカンによる調整が必要不可欠となってくるのだ。CAE全盛の時代にあっても、匠の技が必要な分野なのである。
からの記事と詳細 ( 内燃機関超基礎講座 | レーシングエンジンの熱交換器。設計製造は「非常識」との戦い - MotorFan[モーターファン] )
https://ift.tt/F6gQ9GE
0 Comments:
Post a Comment